1 L/D=10~20,屬于一般深孔。常在鉆床或車床上用接長麻花鉆孔加工。
2 L/D=20~30,屬于中等深孔。常在車床上加工。
3 L/D=30~100,屬于特殊孔深。必須使用深孔鉆在深孔鉆床或?qū)S迷O(shè)備上加工。
2. 切削熱不易傳出。
3.排屑較困難,如遇切削阻塞則會(huì)引起鉆頭損壞。
4.因鉆桿長、剛性差、易振動(dòng),會(huì)導(dǎo)致孔軸線偏斜,影響到加工精度及生產(chǎn)效率。
深孔鉆的類型、使用范圍及工作原理,深孔鉆按排屑方式分為外派屑和內(nèi)排屑2種,外排屑有槍鉆、整體合金孔鉆(可分為有冷卻和無冷卻孔2種):內(nèi)排屑又分為BTA深孔鉆、噴吸鉆和DF系統(tǒng)深孔鉆3種。(下面我們來介紹下曲軸油孔工藝)
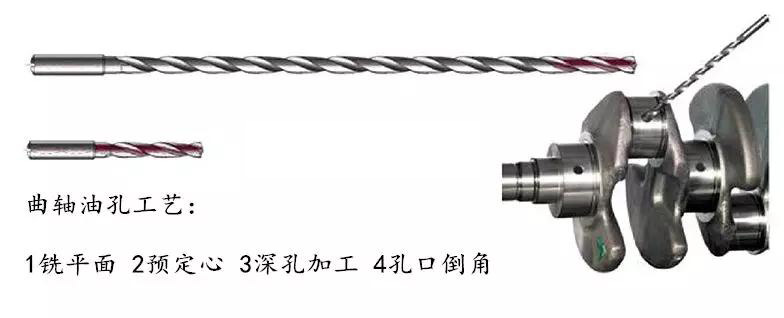
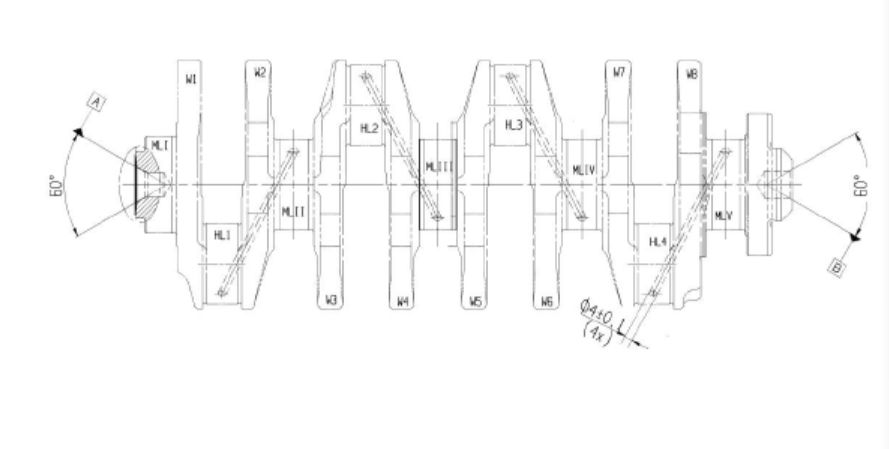
第二步:選擇引導(dǎo)鉆在連桿或主軸上鉆入1.5D-2D的孔深(為后序深孔鉆提供良好的導(dǎo)向和預(yù)鉆準(zhǔn)備)。
第三步:選擇深孔鉆頭在已有的孔徑上鉆通該孔徑。
第四步:(主軸/連桿頸)孔口倒角,去除孔口毛刺。
PS:曲軸油孔工藝一般分為兩種類型,
1、交叉孔:連桿油孔和主軸油孔相互交叉。
(加工有難度)
2、直通孔:連桿有油孔,主軸無油孔。
上面描述的油孔工藝是很多工廠采用的普遍方式,也有的工廠把第一步和第二步合并了,用平底鉆當(dāng)做引導(dǎo)鉆的方式進(jìn)行預(yù)定心(這里不建議工廠采用這種形式),貌似加工的效率提高了,其實(shí)后面的刀具維護(hù)成本會(huì)增加,請(qǐng)注意。(有需要油孔加工程序的可以聯(lián)系小編我,提供程序供您研究)
- 一般平底鉆和引導(dǎo)孔的長短很接近,在更換刀具的時(shí)候請(qǐng)操作者要看清楚,否則容易發(fā)生撞刀事件。
- 倒角鉆在加工孔口倒角的時(shí)候,孔口倒角的大小會(huì)有差別,一般是新刀換刀后,一般是刀具磨損劇烈情況,(換刀/程序中修改參數(shù)可以改正過來)。
- MQL流量變小,這個(gè)會(huì)導(dǎo)致深孔鉆斷裂,產(chǎn)品報(bào)廢,(點(diǎn)檢可以發(fā)現(xiàn)這類問題,油品日常的消耗也可以發(fā)現(xiàn))。
- 修磨回來的深孔鉆在裝刀前,要看內(nèi)冷孔是否有阻塞現(xiàn)象。
1.深孔加工操作要點(diǎn)
主軸和刀具導(dǎo)向套、刀桿支撐套、工件支撐套等中心線的同軸度應(yīng)符合要求;切削液系統(tǒng)應(yīng)暢通正常;工件的加工端面上不應(yīng)有中心孔,并避免在斜面上鉆孔;切削形狀應(yīng)保持正常,避免生成直帶狀切削;采用較高速度加工通孔,當(dāng)鉆頭即將鉆透時(shí),應(yīng)降速或停機(jī)以防損壞鉆頭。
2.深孔加工切削液
深孔加工過程中會(huì)產(chǎn)生大量的切削熱,并不易擴(kuò)散,需要供給充足的切削液潤滑冷卻刀具。一般選用1:100的乳化液或極壓乳化液,需要較高加工精度和表面質(zhì)量或加工韌性材料時(shí),選用極壓乳化液或高濃度極壓乳化液,切削油的運(yùn)動(dòng)粘度通常選用(40)10~20 cm2/s,切削液流速為15~18 m/s ;加工直徑較小時(shí)選用粘度低的切削油;要求精度高的深孔加工,可選用切削油配比為40%煤油+20%氯化石蠟。
切削液的壓力和流量與孔徑及加工方式有著密切的關(guān)系。
外排屑深孔鉆切削液的壓力與流量
孔徑/mm
壓力/Mpa
流量/(L/min)
4-10
2.5-6
8-20
10-15
2-5
20-30
15-20
1.5-4.5
30-40
25-20
1.5-4
40-50
25-30
1.5-3
50-60
內(nèi)排屑深孔鉆切削液的壓力與流量
孔徑/mm
壓力/Mpa
流量/(L/min)
8-15
5-6.5
20-50
15-25
4-5.5
50-70
25-35
3-4.5
70-100
35-45
2.5-4.5
100-125
45-80
2-3
125-200
3.使用深孔鉆注意事項(xiàng)
折斷-開始加工時(shí)
原因
排除措施
設(shè)
備
原
因
檢查進(jìn)給機(jī)構(gòu)(是否進(jìn)給太快);檢查工件是否夾緊或有松動(dòng);防止偏擺,套筒安裝是否正確.
鉆
頭
原
因
修磨是否有問題.
套
筒
端
面
原
因
檢查是否漏油和有沒有切削液卡在端面處.
折斷-鉆削時(shí)
原因
排除措施
設(shè)
備
原
因
檢查進(jìn)給機(jī)構(gòu)(是否進(jìn)給太快);檢查工件是否夾緊或有松動(dòng);防止偏擺,套筒安裝是否正確.
刀
具
損
傷
大
參考刀具壽命部分.
折斷-鉆通時(shí)
原因
排除措施
進(jìn)
給
速
度
退刀時(shí)軸向推力減小,進(jìn)給速度太快,降低進(jìn)給速度.
折斷-退刀時(shí)
原因
排除措施
被加
工工
件形
狀
檢查快鉆通部分的孔是否鉆歪.
刀具壽命-壽命短
原因
排除措施
鉆削
條件
不合
理
邊框/背景是設(shè)置在單元格上的.
設(shè)
備
原
因
主軸偏擺是否過大,檢查主軸和導(dǎo)向套是否同心,導(dǎo)向套和鉆柄的間隙是否太大;防止偏擺,套筒的安裝是否正確.
刀
具
原
因
鉆尖角和導(dǎo)向塊選擇是否正確;鉆頭長度是否比需要長度太多;重磨是否符合要求(砂輪粒度是否太粗,崩刃未磨掉).
切
削
液
原
因
切削液的選擇是否正確(添加劑,粘度等);切削液的過渡是否良好;油溫太高時(shí)應(yīng)增加郵箱容積.
被
加
工
材
料
材質(zhì)性質(zhì)是否均勻.
加工精度-表面粗糙度
原因
排除措施
切削
條件
不正
確
降低進(jìn)給速度.
設(shè)
備
問
題
檢查主軸偏擺,進(jìn)給速度的均勻性,導(dǎo)向套精度,工件是否夾緊.
刀
具
問
題
鉆頭是否夾持是否松動(dòng).
切
削
液
問
題
切削液的選擇是否正確,選擇適當(dāng)?shù)那邢饕?;充分過渡切削液.
加工精度-圓柱度/圓度/擴(kuò)孔超差
原因
排除措施
切削
條件
不正
確
選擇適當(dāng)?shù)倪M(jìn)給速度.
設(shè)
備
問
題
提高導(dǎo)向套精度和導(dǎo)向套與主軸的同心度.
刀
具
問
題
選擇適當(dāng)?shù)你@尖形狀,角度.
切
削
液
問
題
選擇適當(dāng)?shù)那邢饕?
加工精度-彎曲
原因
排除措施
設(shè)
備
問
題
提高導(dǎo)向套精度和導(dǎo)向套與主軸的同心度;穩(wěn)定地夾緊被加工件.
刀
具
問
題
選擇合適的鉆尖形狀,角度和導(dǎo)向塊.
設(shè)
備
問
題
檢查表面是否有切屑,砂眼;檢查表面是否有斜度,將表面加工平整.
被加
工工
件材
料問
題
檢查表面是否有切屑,砂眼;檢查表面是否有斜度,將表面加工平整.
切屑處理-切屑堵塞/纏屑
原因
排除措施
切削
液壓
力低
正確選擇切削液壓力.
切削
液流
量小
正確選擇切削液流量;檢查切削液粘度是都太大,降低粘度.
切屑
形態(tài)
不理
想
切屑很硬時(shí),降低進(jìn)給速度;正確選擇鉆尖形狀,角度.
設(shè)
備
問
題
增大容屑空間.
絲
狀
切
屑
提供進(jìn)給速度,檢查鉆尖切削刃轉(zhuǎn)角處磨損是否太大;檢查鉆尖切削刃轉(zhuǎn)角處切削刃是否崩刃;重磨時(shí)的砂輪粒度是否太粗;鉆中心孔時(shí)產(chǎn)生絲狀切屑,提高切削液壓力,降低進(jìn)給量.
鋸
齒
狀
切
屑
檢查鉆尖或靠近鉆尖處的切削刃是否崩刃.